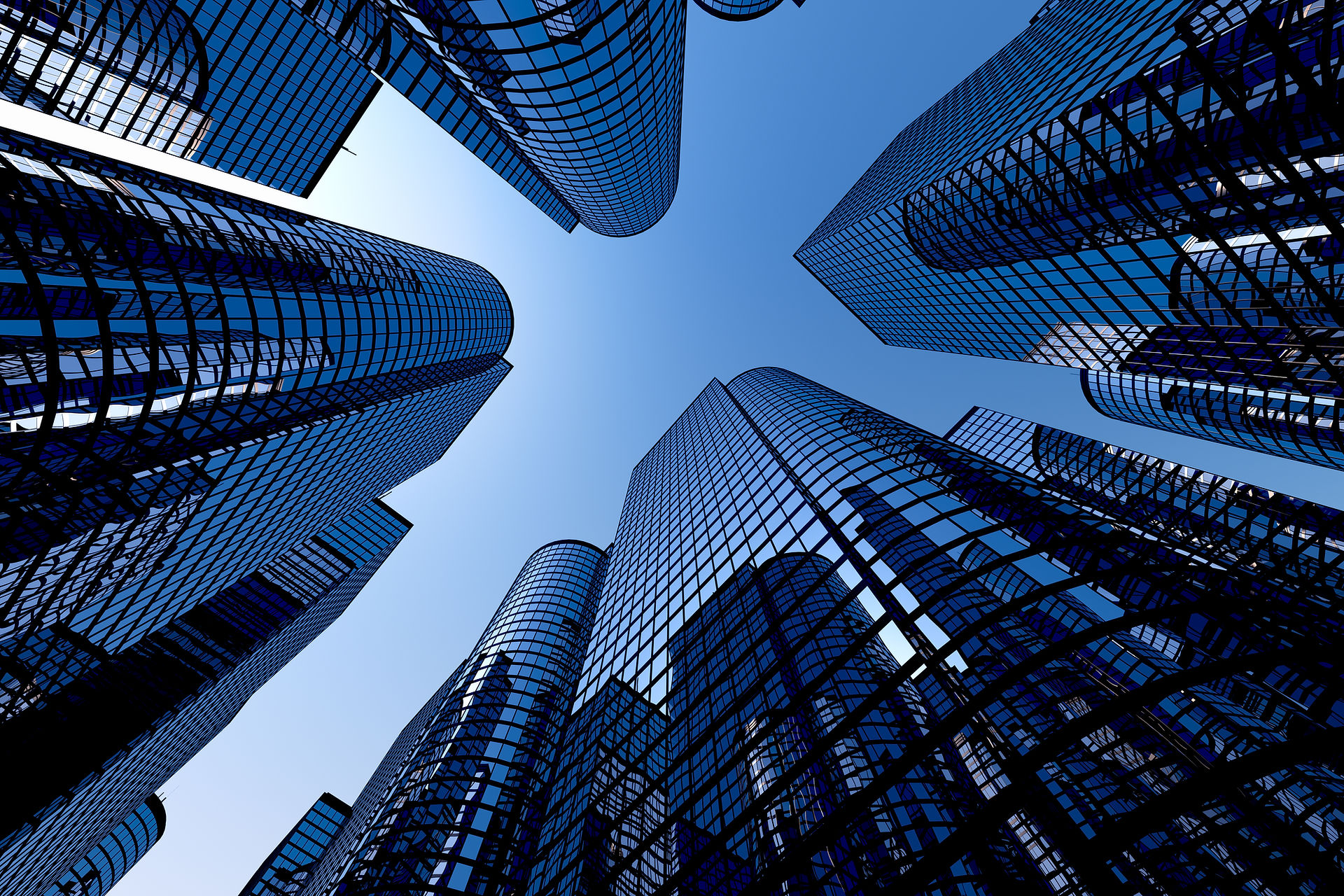

Empower Growth
Build a Competitive Advantage Through Process Quality
ORGANIZATIONAL CERTIFICATION IN PROCESS QUALITY
Naburva is an independent body that has pioneered the idea of organizational certification in process quality based on Lean Six Sigma methodology. The Lean Six Sigma approach is used world-wide by organizations who aim to optimize their business operations. This is a statistics-based methodology that focuses on removal of waste from a process, measuring process variability, and reducing anomalies in measurements that result from special causes.
Unlike other industrial certifications in quality, ours does not aim at laying down unilateral standards and demanding compliance to them, regardless of whether they make sense for a client or not. Rather it is about building the capacity of our clients so they can take ownership of their process improvement initiatives in line with their organizational objectives, industry requirements, and market needs.
​
APPROACH
​
Our approach revolves around the idea of enablement rather than creating non-productive dependencies. We develop a team of Lean Six Sigma experts within the organization, conduct a process analysis, provide customized management tools that are relevant to the client's core business operations, and issue the certification after the organization is ready to take the ball and run with it. The certification does not require annual renewals, periodic submission of compliance documentation, etc. And the reason is simple – an approach that results in cost savings and optimization of processes for an organization, does not require external monitoring for conformity, rather the clients themselves have the core interest and motivation to comply with the Lean Six Sigma principles.
​

​
BENEFITS
​
Naburva's certification in process quality is a symbol of commitment that an organization puts into maintaining the highest standards of performance in its operations. The benefits of the certifications include the following:
​
​
Cost Savings
​
The biggest benefit of adopting a holistic, organization-wide commitment to Lean Six Sigma methodology is cost saving. Most of the business entities have a 'hidden factory' within their operations without the management even knowing about it. This hidden factory costs a huge amount of money wasted on defects, rework, over-processing, excessive inventory pile-up, etc. Since accounting systems do not typically track these costs, management does not even realize if there is anything that needs to be fixed. Organizations such as Motorola, General Electric, U.S. Army, Bank of America, Caterpillar, Honeywell International, etc. have successfully implemented Lean Six Sigma, saving multi-millions, even billions of dollars in operational costs.
​
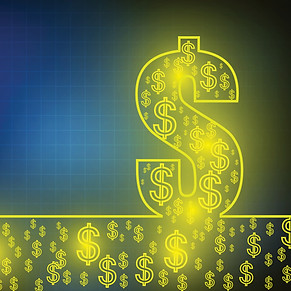

​
Reduced Process Variability​
Besides eliminating waste from a process, Lean Six Sigma philosophy also focuses on reducing its variability, a factor that determines the quality of a process. Enhanced process quality invariably leads to better product quality, whether goods or services. The more a product conforms to its given specifications, the better it is able to meet the customers' expectations.
​
​
Increased Productivity​
The identification and elimination of wastage from a process, and reduction of process variability invariably leads to optimal allocation of resources where needed. This results in increased productivity. Whether a company operates in healthcare, manufacturing, service delivery, or virtually any sector, its management always aims to enhance the productivity of the organization. Implementation of Lean Six Sigma methodology directly leads to an increased level of productivity.
​


​
Enhanced Brand Reputation​
A product that meets the expected standards is bound to result in customers' satisfaction. At the end of the day, it is the customers' trust in the quality of a company's products that determines the position of that organization in the industry, its growth, its share value, and even its very existence. By adopting Lean Six Sigma approach in its operations, an organization ensures that it fulfills the expectation its customers have from its products. Our certification is not only a symbol of process quality internal to an organization, rather our clients can proudly boast of their commitment to quality through their marketing activities aimed at establishing a strong brand image.
​
​
Culture of Continuous Improvement​
Adoption of Lean Six Sigma philosophy at an organizational level leads to promotion of a culture in which members at all hierarchical levels within the organization pursue incremental improvement in their respective functions. Status quo has no place in this culture, and members continuously strive to make their processes better and efficient, one step at a time. Needless to say that an organization with such a culture is always ahead of the game.
​
